5 Top Tips for Preventive Maintenance in Industrial Properties
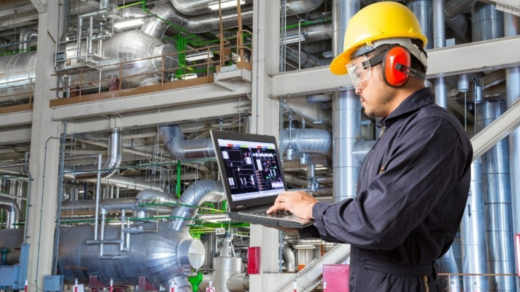
Preventive maintenance is one of the most important aspects of keeping an industrial property running smoothly. It helps reduce unexpected breakdowns, extend the life of equipment, and save money in the long run.
By following a few simple tips, property owners can ensure their machines and systems are in good working condition and avoid costly repairs. In this article, we will discuss five top tips for preventive maintenance that can make a significant difference in your industrial property.
1. Regular Inspections and Monitoring
One of the best ways to prevent problems is to spot them early. Regular inspections and monitoring of equipment, machines, and systems can help identify small issues before they become big ones. Schedule a time each month to inspect your equipment.
Check for signs of wear, unusual sounds, leaks, or changes in performance. Keeping an eye on things can help prevent serious breakdowns and save you from unexpected repair costs.
2. Schedule Timely Industrial Heat Pump Maintenance
Industrial Heat Pump play a crucial role in keeping your industrial property at the right temperature. Just like any other equipment, they need regular maintenance to run efficiently. A well-maintained heat pump will last longer, use less energy, and perform better.
Be sure to clean the filters, check the refrigerant levels, and inspect the system for any damage. Regular maintenance can also prevent problems such as overheating or freezing, which can cause costly repairs. If you’re unsure how to maintain the heat pump, consider hiring a professional to do it for you.
3. Follow Manufacturer Recommendations
Each piece of equipment comes with a manufacturer’s manual that includes important guidelines on maintenance schedules and procedures. It’s essential to follow these instructions to keep the equipment in optimal condition.
Manufacturer recommendations usually cover things like lubrication, part replacements, and cleaning schedules. By sticking to these guidelines, you ensure that the machines are working properly and safely, which can prevent breakdowns and extend their lifespan.
4. Hire an Industrial Maintenance Mechanic
Hiring a skilled industrial maintenance mechanic is a wise investment for any industrial property. These professionals have the expertise to spot issues that might not be visible during regular inspections. They can also provide advanced repairs and maintenance that might be needed to keep complex systems running smoothly.
Whether it’s for regular servicing or emergency repairs, having an experienced mechanic on hand can help prevent costly downtime. Make sure the mechanic you hire is licensed and has a good reputation for providing quality service.
5. Keep a Detailed Maintenance Log
Tracking your maintenance activities in a detailed log is an effective way to stay on top of things. Write down the dates, tasks performed, and any parts replaced or repaired. This log helps you stay organized and ensures that nothing gets missed.
It also provides a record that can be useful for warranty purposes or if issues arise later on. A well-maintained log gives you a clear picture of your property’s maintenance history, making it easier to manage future tasks.
Conclusion
Preventive maintenance is essential for keeping industrial properties running efficiently and safely. By following these five tips—regular inspections, timely heat pump maintenance, following manufacturer guidelines, hiring skilled mechanics, and keeping detailed maintenance logs—you can avoid costly repairs and downtime.
Preventive maintenance not only saves money but also improves the overall lifespan of your equipment. Stay proactive, and your industrial property will remain in great shape for years to come.