How O Rings Enhance Performance in Hydraulic Systems
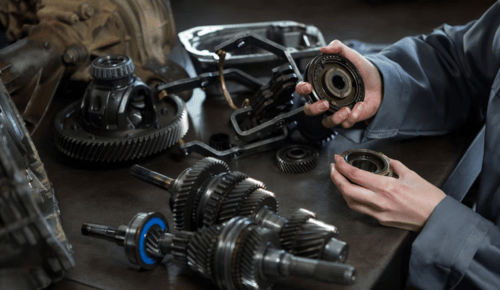
Hydraulic systems rely on precision and efficiency. Every component plays a role in ensuring smooth operation, and sealing elements are critical. Among these, O rings are small but essential. They prevent leaks, maintain pressure, and enhance system longevity.
Their simple design makes them highly effective. They fit between two parts, creating a tight seal under pressure. Without them, hydraulic systems would lose fluid, reducing efficiency and increasing maintenance costs.
Role of O Rings in Hydraulic Sealing
Sealing is crucial in hydraulic applications. Any fluid loss affects performance and causes system failures. O rings form a reliable barrier, preventing leaks in high-pressure environments.
Made from elastomeric materials, they compress between surfaces, filling microscopic gaps. This prevents hydraulic fluid from escaping and ensures consistent pressure. In dynamic applications, they endure movement without compromising the seal.
Material Selection for O Rings in Hydraulic Systems
Choosing the right material determines performance and durability. O rings come in various compositions, each suited for different hydraulic conditions.
Nitrile rubber is common due to its resistance to oil and fuel. Fluorocarbon options handle extreme temperatures and harsh chemicals. Silicone o rings offer flexibility but are less durable in high-pressure systems. Selecting the right material ensures long-lasting performance and minimizes failures.
O Rings Improve Efficiency in Hydraulic Applications
Efficiency is key in hydraulic operations. Fluid power must transfer without loss, and O rings play a vital role in maintaining this efficiency.
A well-sealed system reduces energy waste. With proper sealing, hydraulic pumps work with less strain, consuming less power. O rings also prevent contamination by keeping dirt and debris out, further improving system performance.
Durability and Longevity of O Rings Under Pressure
Hydraulic systems operate under extreme conditions. Heat, pressure, and friction constantly challenge components. O rings must endure these factors to ensure reliability.
Premium-grade O rings resist wear and tear. They retain elasticity, preventing cracks and failures. Regular maintenance and using high-quality seals extend their lifespan, reducing replacement costs and downtime.
Preventing Leaks with High-Quality O Rings
Leak prevention is essential for hydraulic efficiency. Even minor leaks lead to pressure drops, wasted fluid, and system malfunctions. O rings provide a cost-effective sealing solution.
They expand under pressure, ensuring a firm seal. Over time, degraded seals cause leaks, but high-quality O rings resist degradation. Regular inspections help identify worn-out seals before they cause issues.
O Rings and Their Impact on Hydraulic System Maintenance
Maintenance is crucial for any hydraulic system. Proper sealing reduces the frequency of repairs and extends component life. O rings contribute to smoother maintenance schedules.
When seals are intact, there’s less need for frequent part replacements. Hydraulic fluid remains clean, preventing contamination-related failures. Investing in durable O rings minimizes repair costs and improves system reliability.
Conclusion
O rings are small but essential for hydraulic system performance. They maintain pressure, prevent leaks, and enhance efficiency. Choosing the right material and performing regular maintenance extends their lifespan.
By ensuring a proper seal, O rings contribute to smoother operations, reduced energy consumption, and lower maintenance costs. Their role in hydraulic applications is undeniable, making them a vital component in any system.